Table of Contents
ToggleWhat is a countersink?
A countersink is an angled taper applied to a hole that allows a fastener (usually a flat head screw or similar) to sit even with, or below the surface which has been countersunk. Occasionally, a countersink is used simply as a method of chamfering or deburring a hole.
Countersink symbol
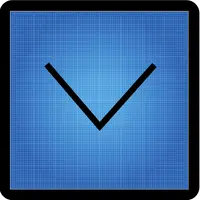
The GD&T callout for a countersink is shown below. Some older blueprints may use the notation CSK to identify a countersink dimension.
If you want to type the ⌵ symbol, hold the ALT key and press 9013. See this list for other common keyboard shortcuts for GD&T and blueprint symbols.
How to dimension a countersink
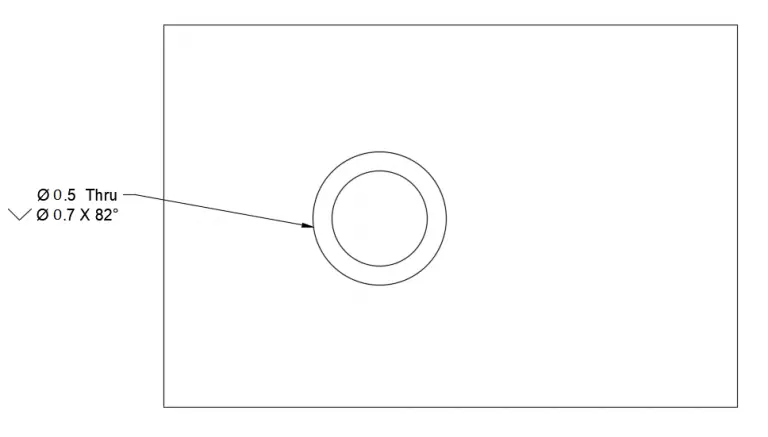
A countersink is dimensioned by specifying the diameter of the countersink where it meets the surface and the included angle. In the above example, the part has a 0.5 thru hole and a countersink with a diameter of 0.7 and an included angle of 82°.
How to measure a countersink
Countersinks can be measured by many different gauges. The easiest tool to use, assuming the tolerances aren’t too tight, is a pocket comparator with a reticle. Optical comparators and CMMs are regularly used to measure countersinks with very tight tolerances.
What does a countersink look like?
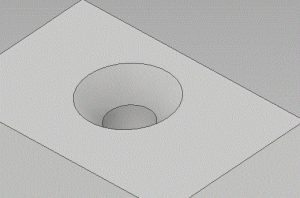
Countersink vs chamfer
A countersink and a chamfer are very similar. A countersink is basically no different than a chamfer on a hole.
The main difference is that a chamfer is normally thought of as being at 45 degrees (though the angle can vary). A countersink is usually one of many different standard angle sizes.
The most common countersink angles are 82°, 90° or 100°.
Note that in the case of the 90° countersink, this callout is the same as a 45° chamfer because the countersink angle takes both sides into account, so it is twice the chamfer angle.
Countersink vs counterbore
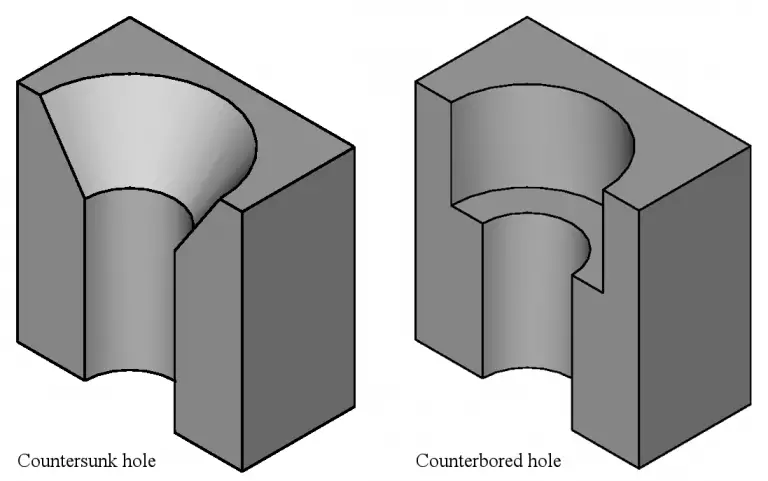
The difference between a countersink and a counterbore is that a countersink has an angled bottom and a counterbore has a flat bottom. Countersinks are often used to recess a flat head screw. Counterbores are used to recess bolts, washers and other fasteners.
Countersink vs spotface
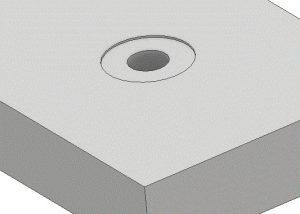
A spotface has a flat bottom like a counterbore while a countersink is angled. A spotface is used to create a flat area in a specific location to allow a fastener such as a screw or bolt to sit squarely.
Want to learn more?
GD&T is a complicated subject and understanding it correctly can be the difference between a perfect part and scrap.
The best way to learn GD&T is from experienced teachers who can break down the material into manageable pieces.
Luckily, we know someone.
And MachinistGuides.com readers get an exclusive discount on training!
Related articles
For more information see these related articles: