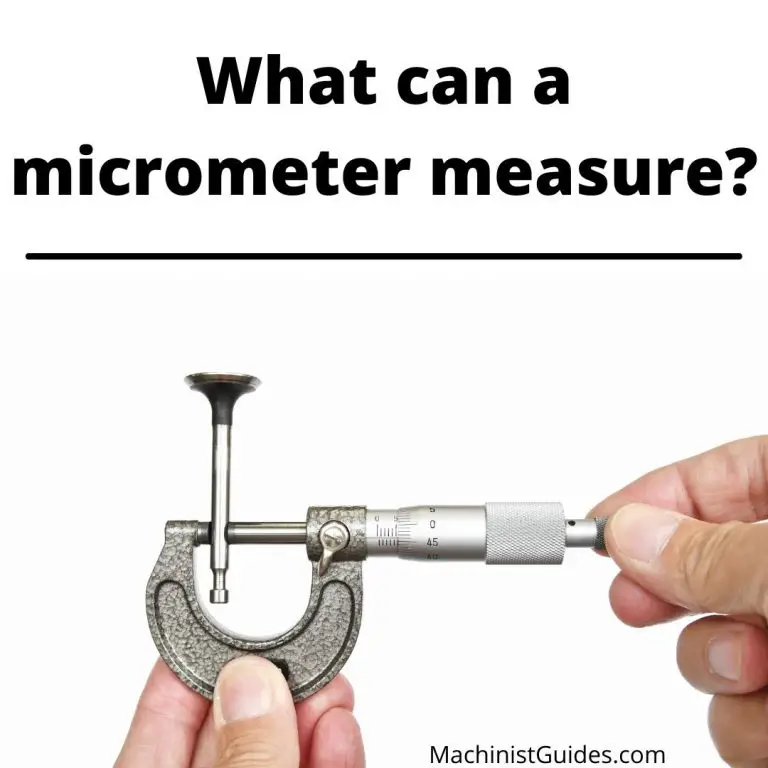
Micrometers can measure a large variety of things, but they do have their limitations.
Those limitations are based on their accuracy and their measuring range as well as the type of micrometer.
Because they are specialized measuring tools, you need to make sure that you use micrometers for the right application and wouldn’t be better off with another measuring tool.
Table of Contents
ToggleHow accuracy affects what a micrometer can measure
Accuracy is one of the most important features of a micrometer.
Micrometers are commonly used to measure parts or features of a part, such as its thickness, to a high level of accuracy. Engine components are just one example of the types of highly accurate parts that micrometers are used to check.
Micrometers that read in inches are commonly accurate to +/- 0.0001” while metric micrometers usually measure to +/- 0.002mm.
There are some that do better and some that do worse, but in general most will measure with the above listed accuracy.
Because they are so accurate, they don’t work well for all measurements. For example, if you need to measure a board for a cut and you only need it accurate to 1/16 of an inch (which equals .0625”), then the micrometer is major overkill. It measures 625 times more accurate than you need!
They are slower too. If you only need accuracy of 1/16 of an inch, then bust out the tape measure, take your measurement and keep on trucking.
Micrometer measuring ranges
The other major limitation of a micrometer is its measuring range.
Inch micrometers measure in increments of 1”. So you will have a 0-1”, 0-2”, 0-3” micrometer and so on. This is why micrometers are often sold as a set with 0-3”, 0-6” and 0-12” sets being the most common.
Having a set of micrometers allows you to take accurate measurements over a larger range of sizes.
Metric micrometers are found in 25mm increments. 0-25mm, 25-50mm and so on. They too are sold as sets to cover larger measuring ranges.
Basically, a micrometer will take a very accurate measurement at the sacrifice of speed and the range of measurements it is capable of.
For many measuring devices you will find that as the accuracy of the tool gets better, the range it can measure over will get smaller.
Types of micrometers
Micrometers are also called screw gauges. There are many different types of micrometers that use the same screw gauge mechanism to measure different types of features. It’s doubtful you need to know about all of them so let’s stick to the basics.
Standard micrometer
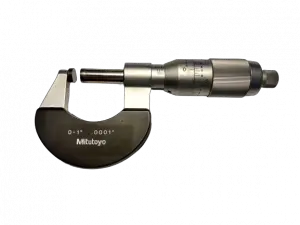
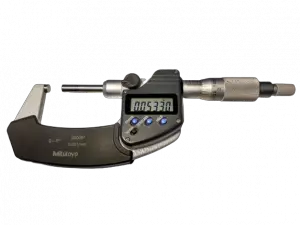
First off is your standard micrometer. If someone simply says micrometer then they are referring to an outside micrometer or ‘mic’.
Outside mics are used to measure external dimensions such as the length, width, or thickness of a part.
They are by far the most common micrometer used.
Inside micrometer
Inside micrometers get used to measure internal features such as hole diameters or slot widths. One thing to know about inside mics is that they are often not as accurate as outside micrometers.
The most common accuracy for an inside micrometer is +/- 0.001”.
Depth micrometer
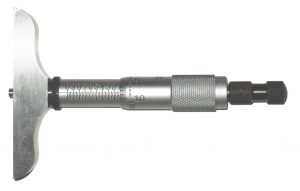
You are never going guess what a depth micrometer measures. Wait… you already know?!
Well thanks for ruining the surprise.
Depth mics measure the depth of features such as holes or slots. Just like an inside micrometer, they are often not as accurate as outside micrometers and usually measure to an accuracy of +/- 0.001”. Their design also means that they can be easier to get an incorrect measurement.
Practice using them on a known standard such as a gauge block is the best way to get good with them.
Accuracy vs resolution
We’ve talked a lot about the accuracy of micrometers, but we haven’t yet talked about their resolution.
Accuracy is how close to a true measurement the micrometer is capable of.
Resolution is how small the graduations that it can resolve are. At times the resolution of a micrometer, especially digital micrometers, may be better than the accuracy which can lead you to believe that you are measuring to tighter tolerances than you actually are.
When comparing micrometers make sure to pay attention to the accuracy of the tool.
Alternatives to micrometers
When it comes to picking a tool other than a micrometer to use, it all comes back to your accuracy needs and the speed of the measurement.
Let’s discuss the two main alternatives to micrometers:
Calipers
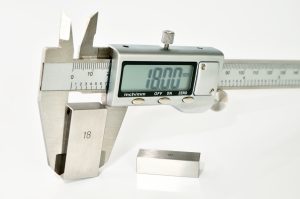
Calipers, whether digital, dial or vernier, are less accurate than micrometers. They typically measure to an accuracy of +/- 0.001”.
But what they sacrifice in accuracy they gain in versatility and speed of measurement.
While micrometers only measure a single type of measurement such as an outside, inside or depth measurement, most calipers will take all three.
They also have a larger measuring range with the most common type being able to take readings from 0-6”. You would need six separate micrometers to match the outside dimension measuring capability of a single set of calipers.
We discussed earlier how micrometers aren’t the fastest measuring tool to use. When compared to calipers this really becomes noticeable. A set of calipers could take dozens of measurements across their entire measuring range in the time it would take to take a few readings with a micrometer.
Calipers compared to micrometers have their advantages and their disadvantages. Pay attention to these differences when deciding which one is right for your measurement.
Dial indicators
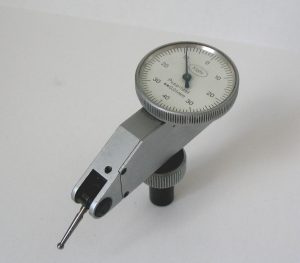
Dial indicators come in a couple different varieties. First is the dial test indicator.
Dial test indicators are used to take comparison measurements. They get set up or “zeroed” to a known standard such as a stack of gauge blocks and measurements are taken relative to that standard.
A dial test indicator will have a relatively small measuring range, usually measured in thousandths of an inch (0.001”) and will measure to a high degree of accuracy such as 0.0001” or better.
They specialize in taking very accurate measurements repeatedly. If they are used to check a variety of measurements, then they will be quite slow to use because they need to be set up for each different measurement.
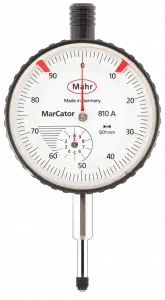
Another type of dial indicator is drop indicator. They most often come with a larger dial face, usually about 2-3” across, and they have larger measuring ranges.
A typical measuring range for a drop indicator is one inch but they do vary and can be smaller or larger. When compared to dial test indicators, they have significantly less accuracy. Most drop indicators are accurate to 0.001”. Their most common application is set up in either a snap gauge or a height stand which allows them to be used to take quick, repetitive measurements.